Shell molding is a metal casting process where molten metal, melted in a medium-frequency induction electric furnace, is poured into a shell.The thin-walled shell is created by injecting a metal pattern with precoated sand to form each half of the shell, and then combining the two halves.
A two-piece metal pattern is created in the shape of the desired part with a pouring cup to introduce molten metal into the ‘shell’. To create a two-part shell, in which two halves are combined to create a full shell, two metal patterns must be produced.
Set temperature, pressure and curing time for the metal pattern. When the pattern is heated to the appropriate temperature, the precoated sand is shot into the cavity. The shell half is then ejected from the metal pattern when it is cool.
The two halves are sealed using glue, or a combination of glue and other fasteners to form a shell which is similar to the ceramic shell used in the investment casting process.
The completed shell is baked at the oven at setting time and temperature.
The subsequent process is the same as the investment casting technology-----
The shell is then placed into a flask and send to the vibrating table. The shell is firmly supported by sand and is ready to get poured.
The metal (steel scrap) is melting in the induction electric furnace and certain alloy is added to each furnace if necessary. Metal is heated to 1530-1580℃ in molten state and is poured into the shell while it is still hot – liquid metal flows into the pouring cup, through the central gating system, and into each mold cavity on the tree. The pre-heated mold allows the metal to flow easily through thin, detailed sections.
Once the metal is sufficiently cooled and solidified inside the shell, it's time for shakeout. Shakeout is basically vibrating the shell and casting so that the shell breaks apart and fall way. After removal, the castings are sent to sand blasting to remove the extra sand on their surface. After that the casting are separated from their gating system tree by using different methods such as manual impact, sawing, cutting, etc.
Finishing operations such as grinding, soldering, sand blasting, machining and straightening are commonly employed to smooth the part at the gates and remove imperfections such as sand holes, slag eyes, flash burrs, bulging, deformation and so on. After passing visual inspection, depending on the part that being cast, heat treating is to be employed to harden the final part.
Qianhao has established a shell molding casting production line in recent years. Comparing it with investment casting, the difference of the two lies only in shell making process, the subsequent process shares the same production line. Shell molding process has the following outstanding advantages, which in some cases can replace investment casting process, and will have better prospects in the future.
1.Shell molding process produces castings whose high dimensional accuracy and good surface finish that are close to those produced by waterglass lost wax process, but are better than those produced by other sand casting process.
2.More environmental friendly in shell making material and process.
3.Higher productivity and lower cost compared with water glass lost wax process.
4.Shorter lead time.
Disadvantages:
Metal pattern cost is high and is only ideal for large volume orders.
Highly complicated shapes cannot be formed.
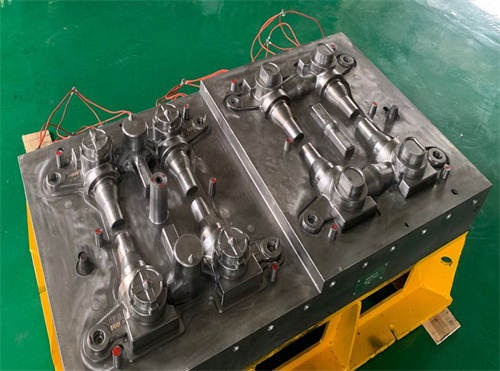
Metal Mould

Automatic Sand Shooting Machine
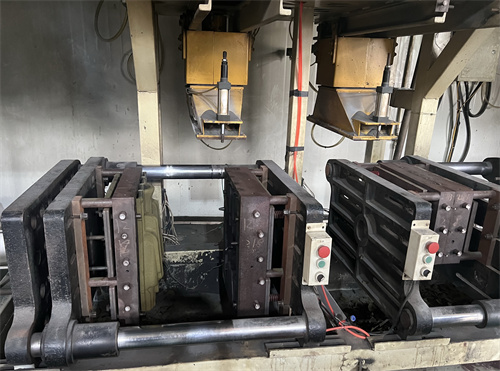
Sand Shooting
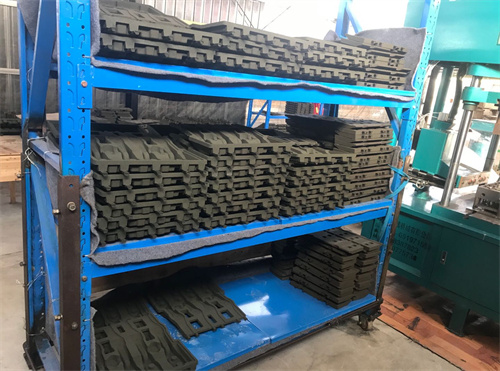
Thin Wall Shell
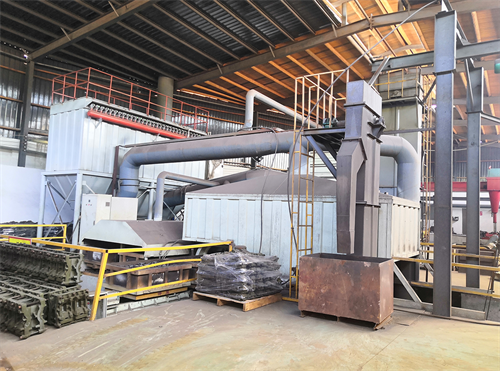
Casting Production Line
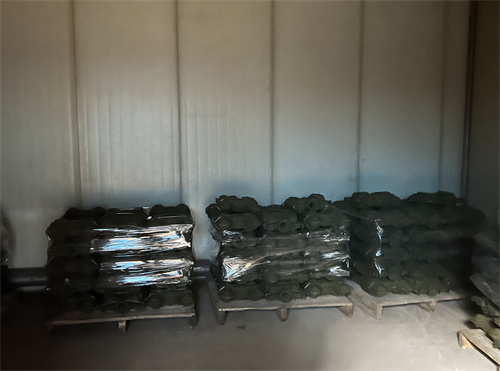
Baking
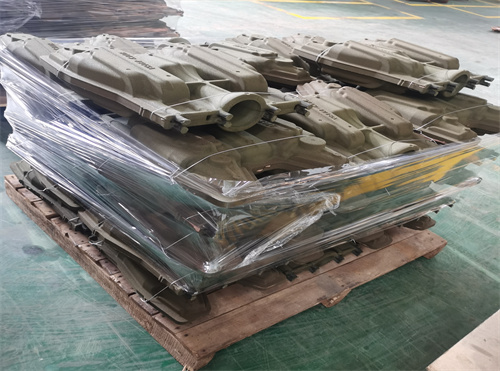
Shell
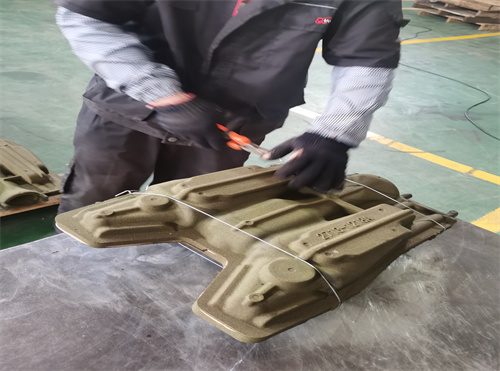
Shell Assembly
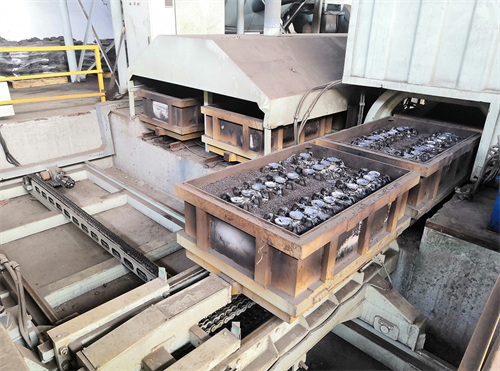
Cooling
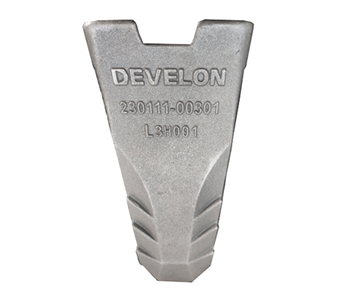
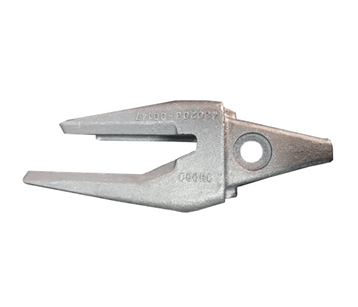
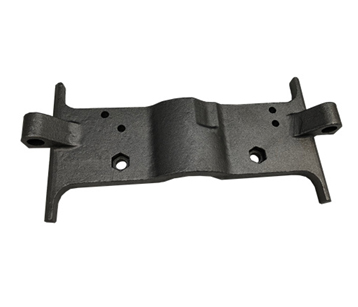
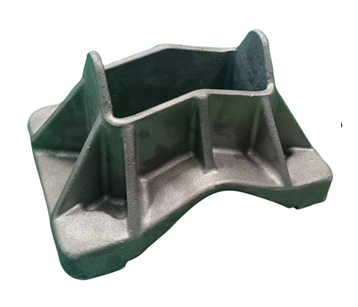
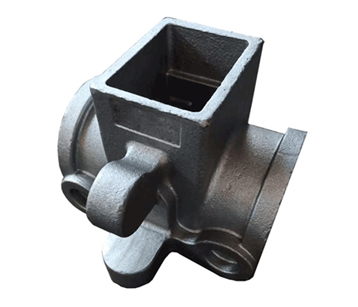
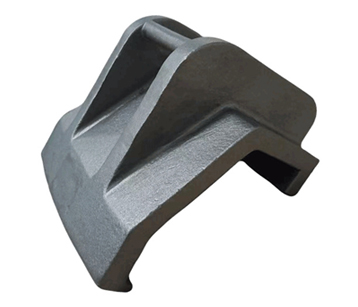