QIANHAO provides superior quality hot forging parts and components for a wide range of industries including automobile, rail, construction equipment, material handling equipment, agricultural machinery,others.
As a major metal fabrication, forging is a metal forming technique that uses localized forces of compression. Forgings have undergone major changes that lead to more efficient, faster and more durable processes. Today’s forging is usually done using electric, hydraulic or compressed air driven forging presses or hammer tools.
Hot forging is known to produce some of the strongest manufactured parts and components compared to other metal manufacturing processes. We produce hot forging parts and components from a few grams to more than a few ten kilograms. For hot forging parts with special surface finish requirements, we provide a broad range of secondary operation including machining, surface finishing, etc.
During hot forging, the temperature reaches above the recrystallization point of the formed metal. As the step of plastically deforming the metal above the recrystallization temperature, these high temperatures are required in order to avoid strain hardening during deformation. This process typically involves heating the metal (above its recrystallization point) and then comminuting it into a mold that can also be heated as needed. Because the metal is hot, it is easy to “move” and enables manufacturers to make more complex shapes than cold forging.
For superalloys, which have low malleability, processes such as isothermal forging (deformation in a controlled atmosphere) are used to avoid oxidation. Isothermal forging, also known as hot forging, is a thermal processing process that keeps a workpiece at its maximum temperature throughout the forming process.
Maintaining this temperature is done by heating the mold – it will be at an elevated or slightly lower temperature of the workpiece. The force applied by the mold forms the workpiece, and because the mold is also at an elevated temperature, the cooling of the workpiece between the mold working interfaces is eliminated. This in turn leads to an improvement in the flow properties of the metal (work piece).
Increased ductility
Complex shapes
Retain the strength of metal
Elimination of defects, inclusions and porosity.
Relative low costs
High production output
Qianhao has the ability to provide carbon steel and alloy steel forgings made by open-die or closed-die forging process.
Open-die forging involves the shaping of heated metal parts between a top die attached to a ram and a bottom die attached to a hammer, anvil or bolster. In open-die forging, the dies do not enclose the workpiece, allowing it to flow except where contacted by the dies.
Closed die forging involves two or more dies that contain a precut profile of the desired component. The heated raw material is placed at the bottom of the die. The dies then move towards each other until the raw material is formed into its required shape and size.
Open die forging is the best choice when large/long components of the material, with high exacting internal conditions (homogeneity), are required. It also suitable for small quantity orders because of low/no investment cost. Compared to the open die forging, the close die forging can achieve more complex geometries, very much close to the dimensions of the finished component. It is used to manufacture series production as this is particularly convenient to absorb the costs the dies. It allows furthermore to use reduced over-dimensions, feature which allows cost savings on input weights as well as on final machining due to less material to remove.
Forging is a favorable and effective manufacturing process. Each time the metal is beaten, impurities are eliminated and the grains becomes finer, the structure becomes more refined and regular and the metal is transformed into a material that is both flexible and strong. Thus forged parts can achieve high degree of strength and flexibility and stand up to the harshest natural environments.
IATF 16949
Jiangxi JH.
Jiangxi Province
Hot Forging
Founded 1970
Factory 680,000SM
Twelve lines (1T,1; 3T,1; 5T,1;10T,1; 2000T,3; 2500T,2; 3150T,1;6300T,2)
980 employees
Annual Capacity 17,0000 tons
Carbon & alloy steel
Max size - 1,200mm Linear x 1,200mm Did
Weight range -0.5 - 800KGS
Tolerance - CT7 - 10
Surface roughness - Ra6.3 - 12.5um
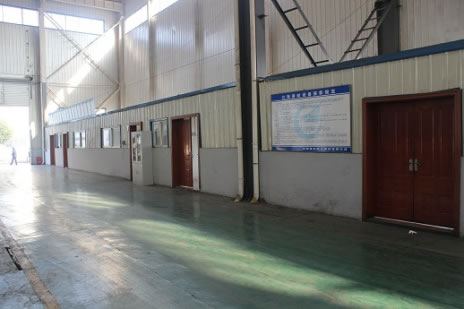
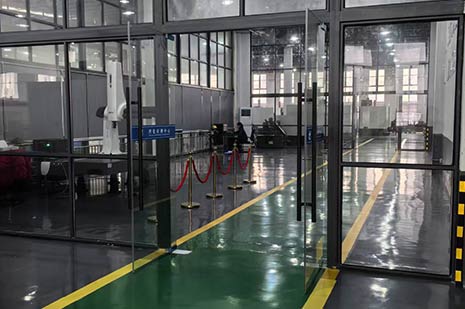
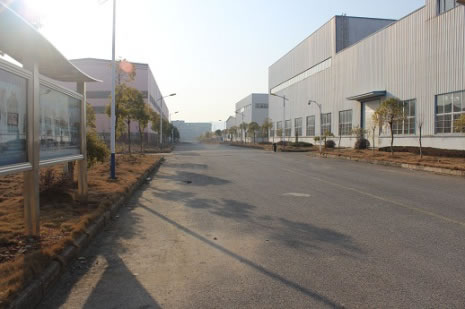

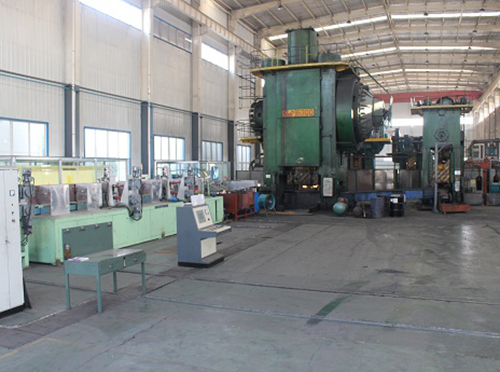
6,300 T Forging Hot Die
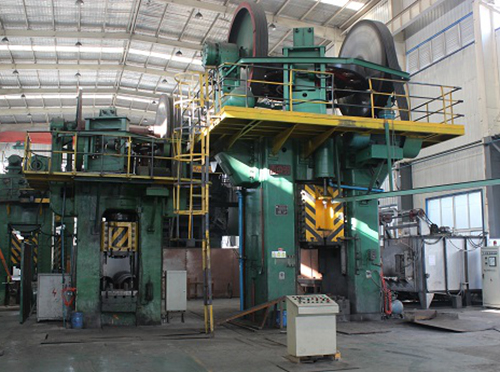
2,500 T Hot Die Forging
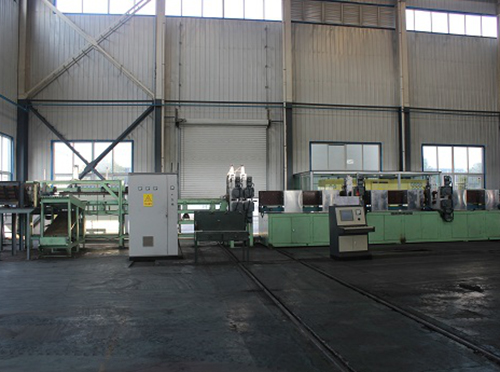
Medium Frequency HT Furnace
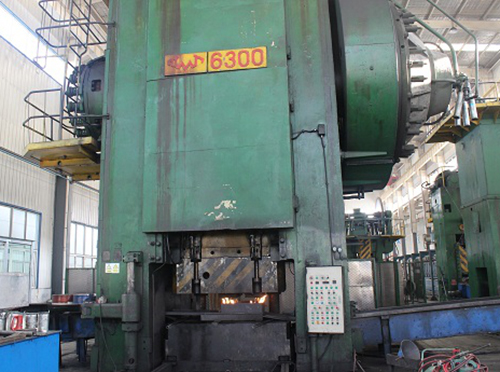
6,300 T Hot Die Forging Machine
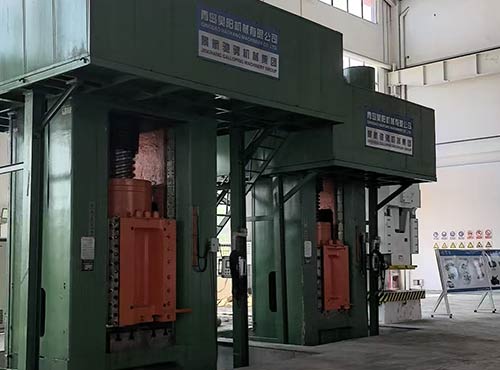
2000T Electric Screw Press
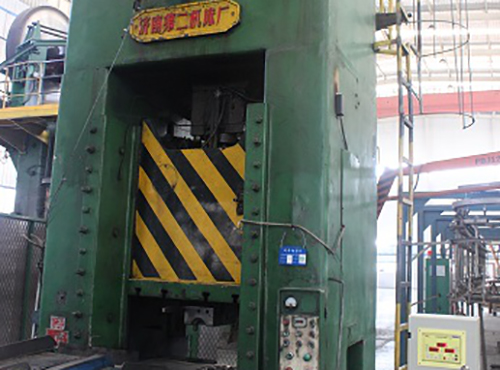
315 T Closed Type Single Point Press
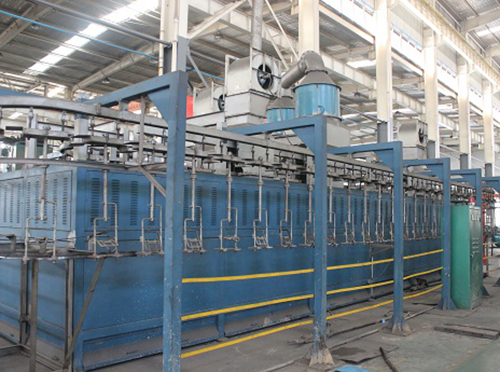
Controlled Quench
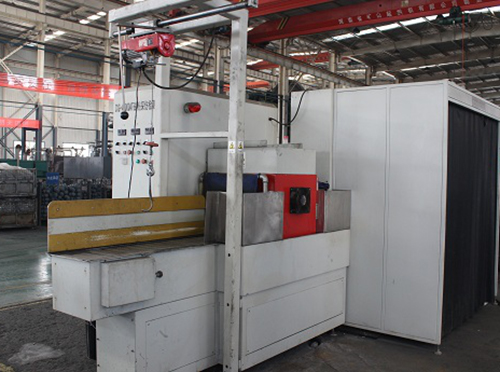
Magnetic Particle Testing
IATF 16949
Zhejiang YL.
Zhejiang Province
Hot forging
Founded 1986
Factory 38,000SM
Six lines (300T,400T,630T,1000T,1600T,4000T)
100 employees
Annual Capacity 25,000 tons
Carbon & alloy steel
Max size - 1,200mm Linear x 230mm Did
Weight range -0.1 - 300KGS
Tolerance - CT7 - 10
Surface roughness - Ra6.3 - 12.5um
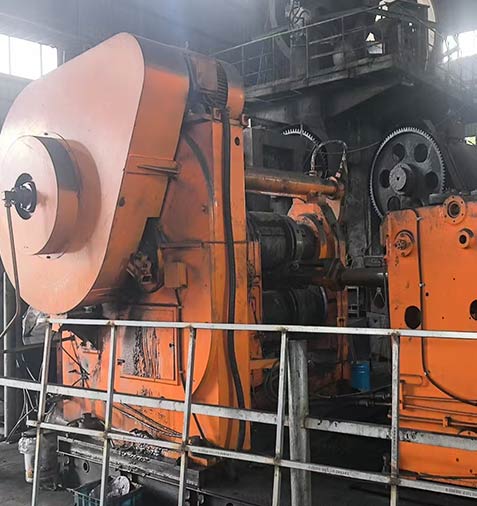
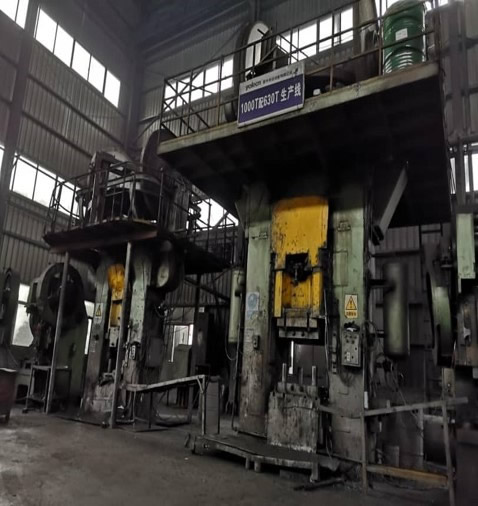
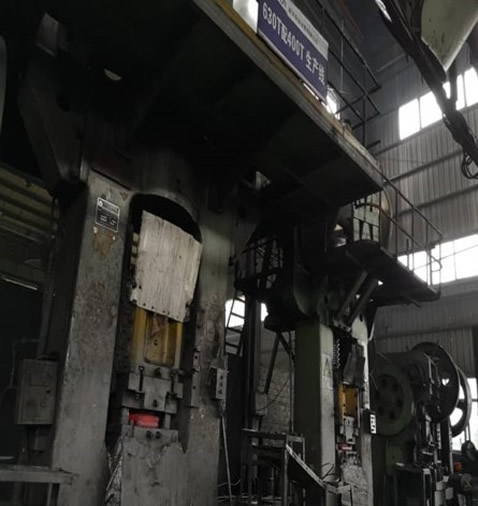
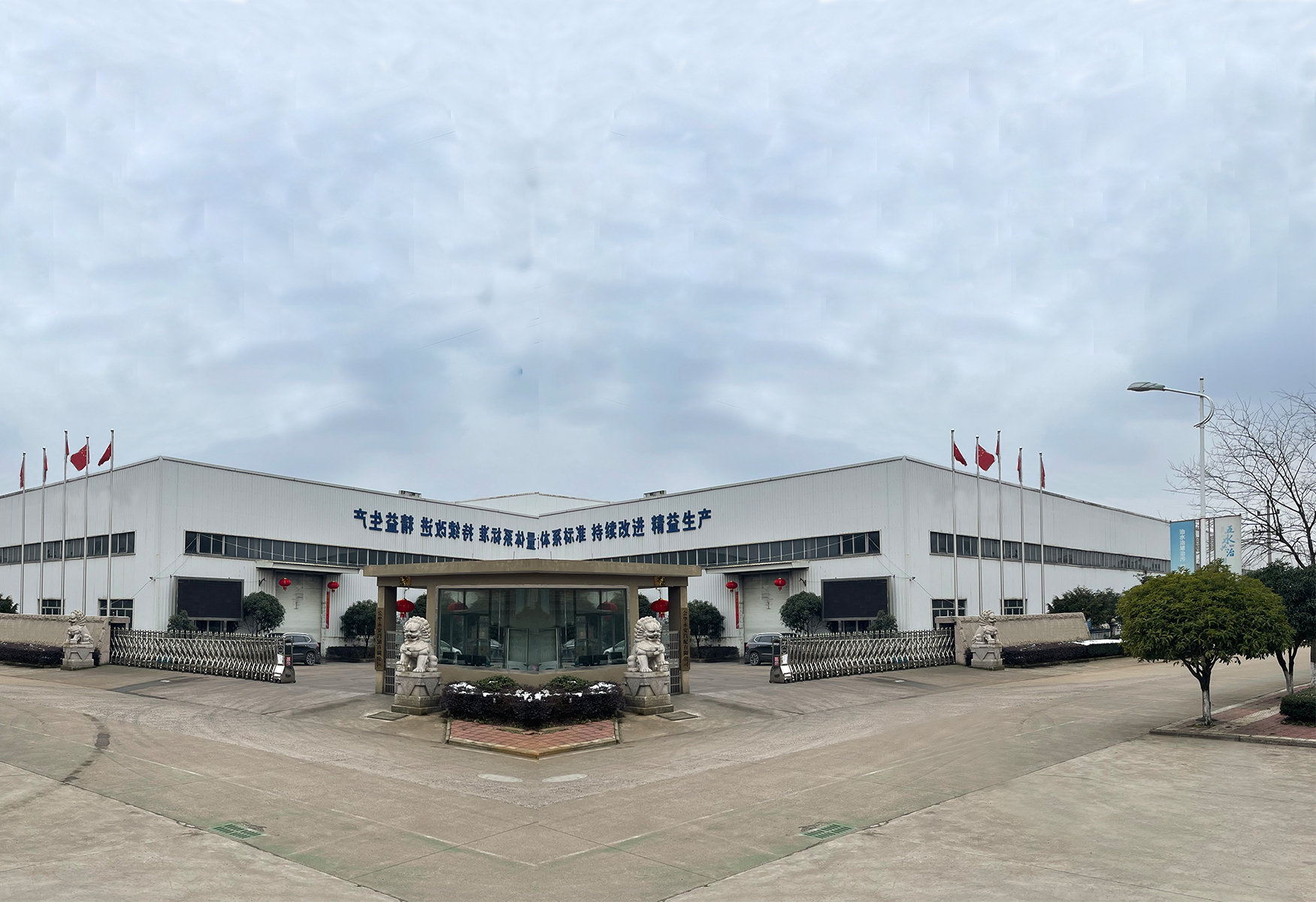
IATF 16949
Zhejiang JX.
Zhejiang Province
Hot forging
Founded 1995
Factory 50,000SM
Eight lines (300T,400T,630T,1000T,2000T,2500T)
200 employees
Annual Capacity 20,000 tons
Carbon & alloy steel
Max size - 800mm Linear x 150mm Did
Weight range -0.1 - 50KGS
Tolerance - CT7 - 10
Surface roughness - Ra6.3 - 12.5um
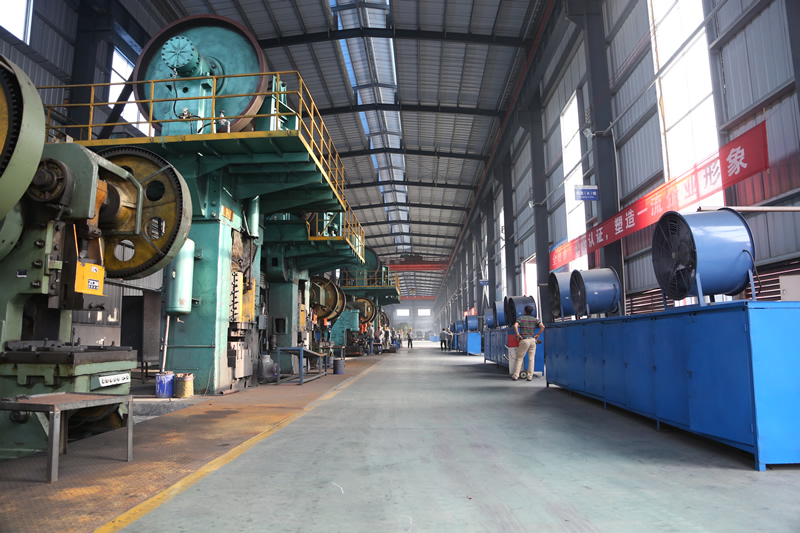
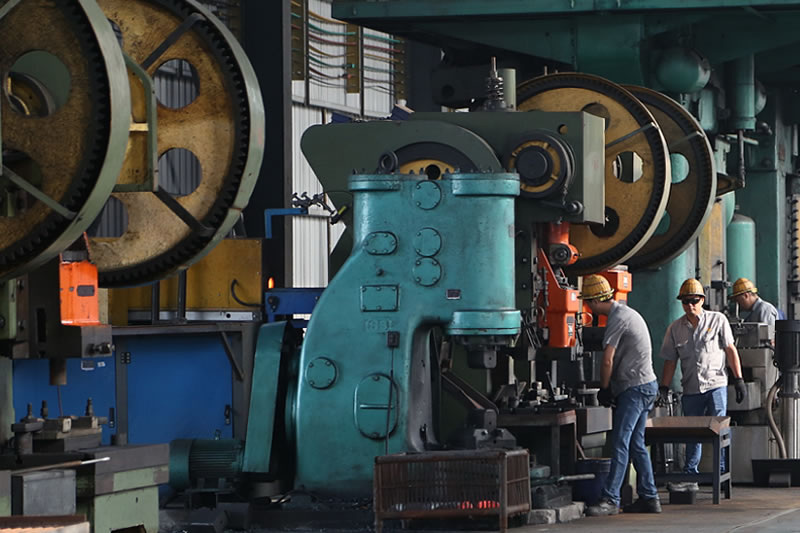
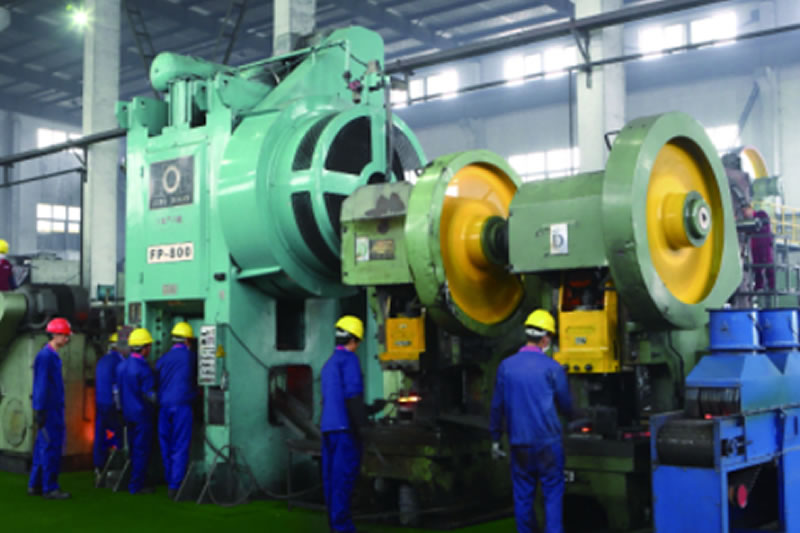

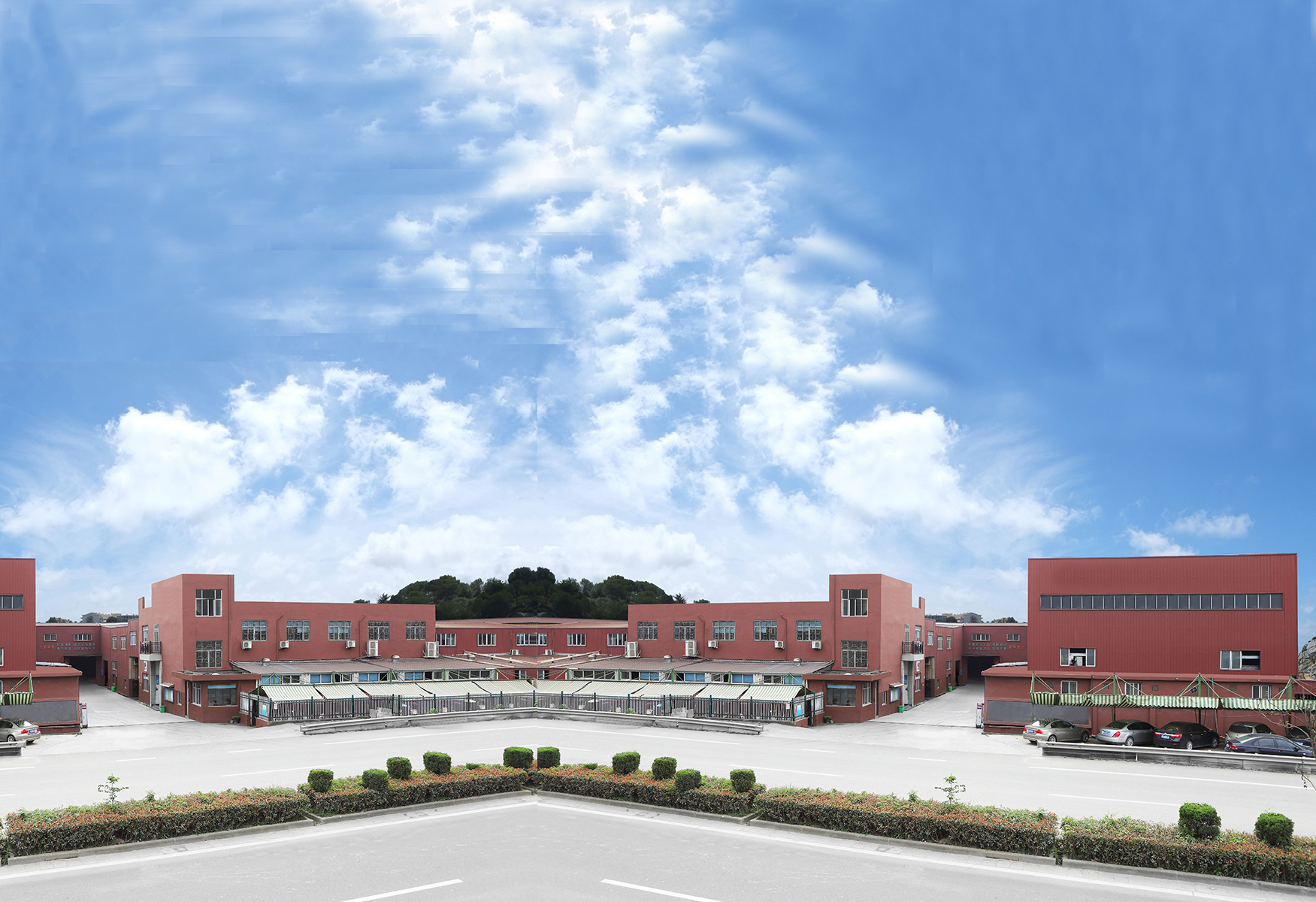
ISO 9001 IATF 16949
Zhejiang JF.
Zhejiang Province
Hot forging
Founded 2005
Factory 3,8000SM
Six lines (400T,630T,1000T,6300T)
120 employees
Annual Capacity 15,000 tons
Carbon & alloy steel
Max size - 1,500mm Linear x 200mm Did
Weight range -0.1 - 450KGS
Tolerance - CT7 - 10
Surface roughness - Ra6.3 - 12.5um
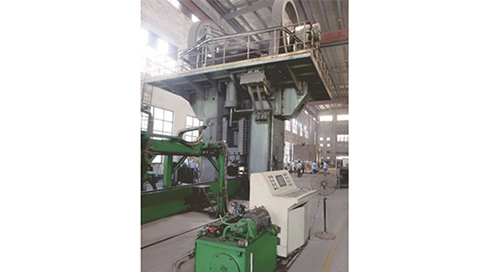
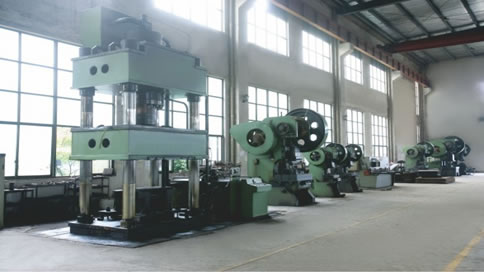
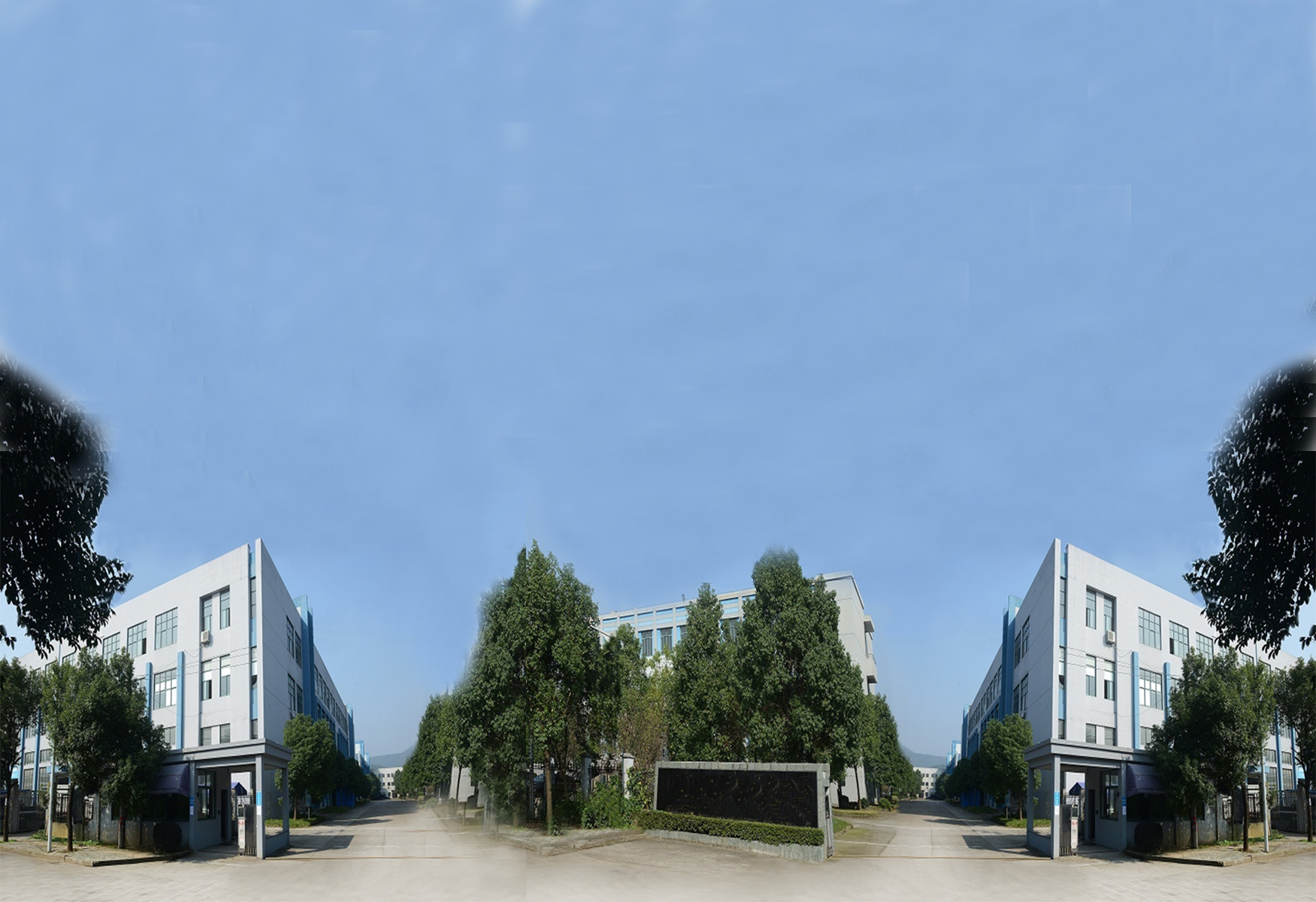
ISO 9001 IATF 16949
Jiangsu CT.
Jiangsu Province
Hot Forging, Warm Forging
Founded 2018
Factory 50,000SM
Eight lines (650T,1600T,2500T,8000T,10000T)
150 employees
Annual Capacity 50,000 tons
Carbon & alloy steel
Max size - 1500mm Linear x 500mm Did
Weight range -0.1 - 400KGS
Tolerance - CT7 - 10
Surface roughness - Ra3.2 - 12.5um
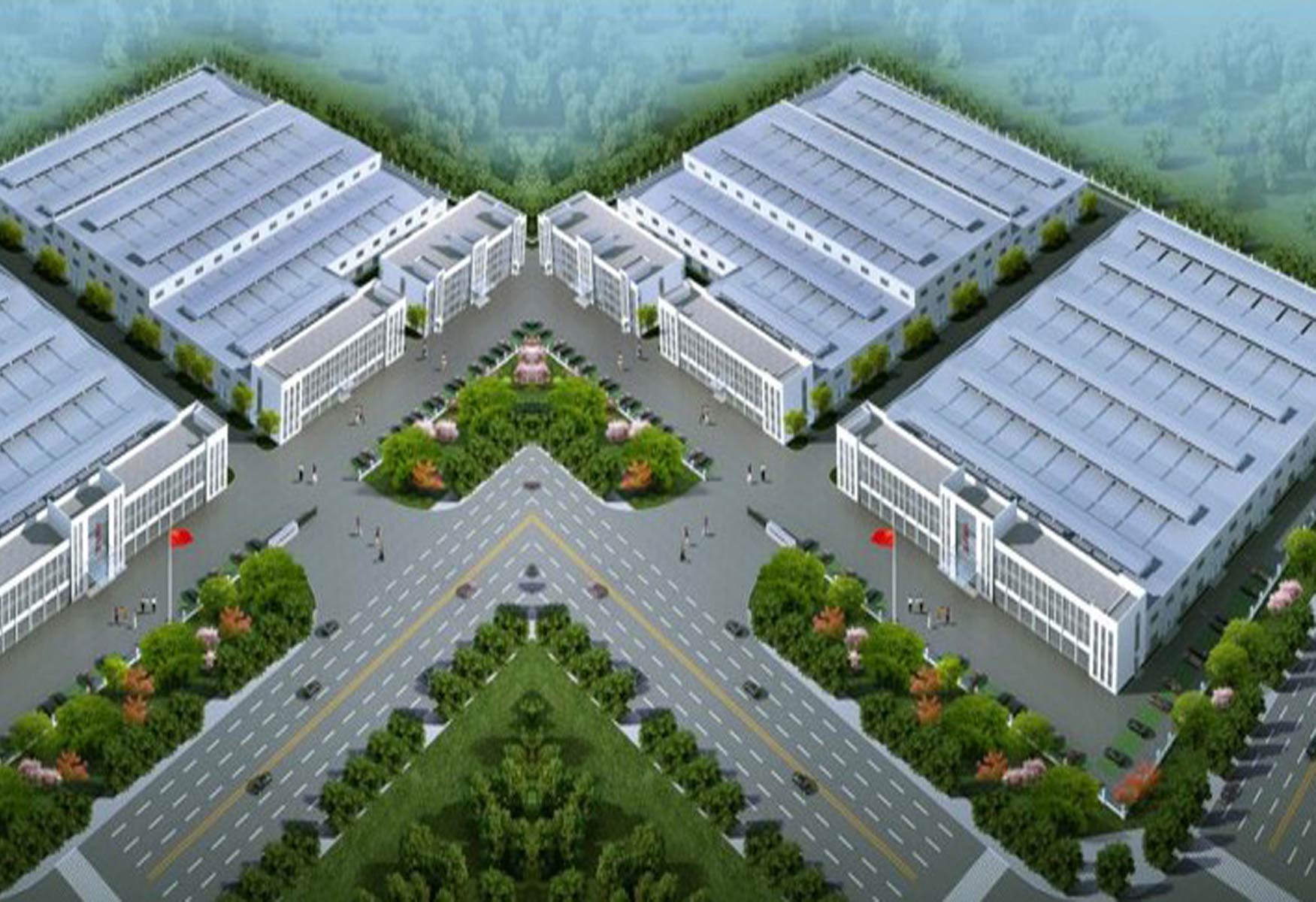
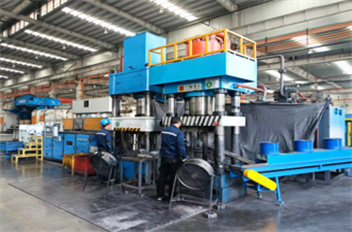
630T Hydraulic Warm Forging Line
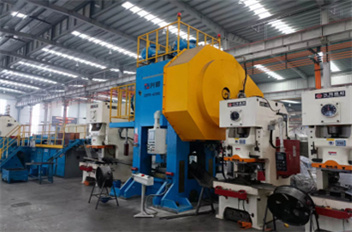
650T Hot Forging Press Production Line
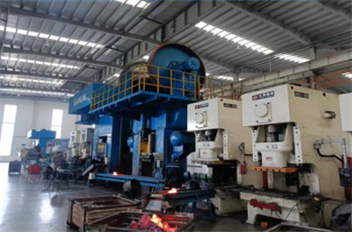
1600T-1000T Forging Press
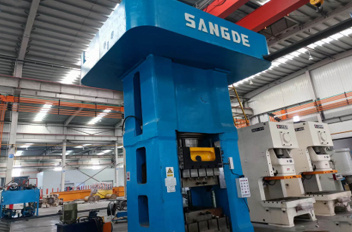
2500T Electric Screw Press Production Line
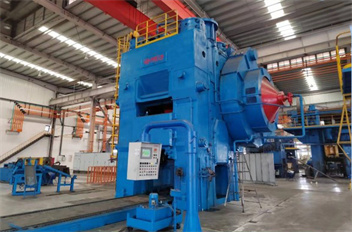
8000T Hot Forging Press

10000T Electric Screw Press Production Line
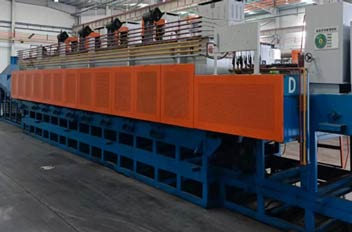
Normalizing Furnace
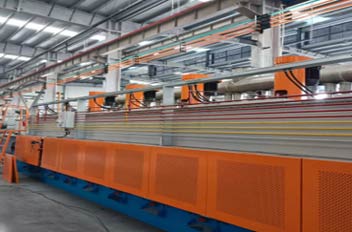
Q&T Furnace
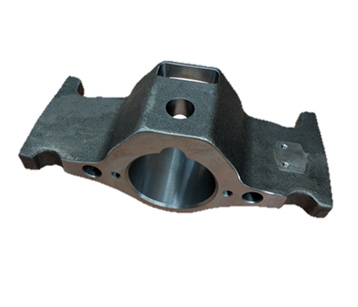
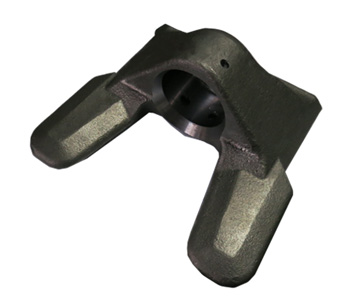
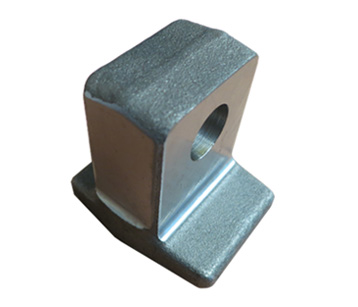
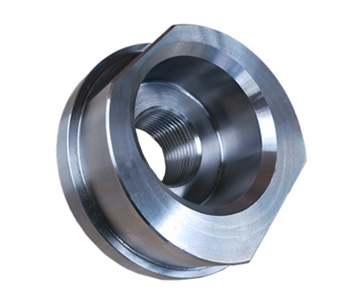
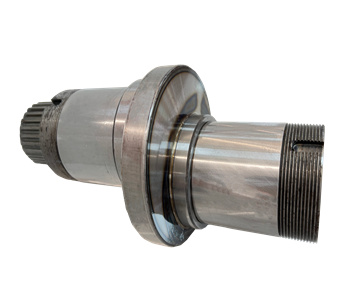
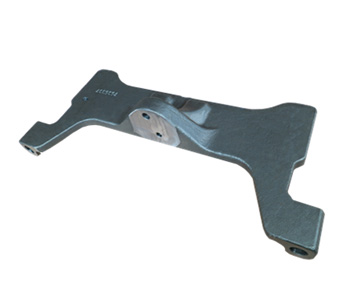
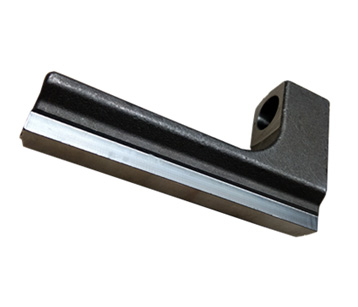
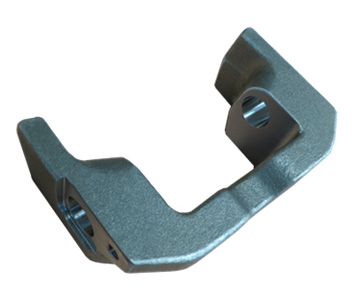
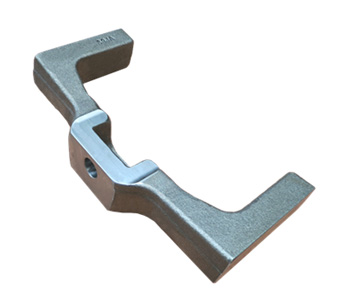
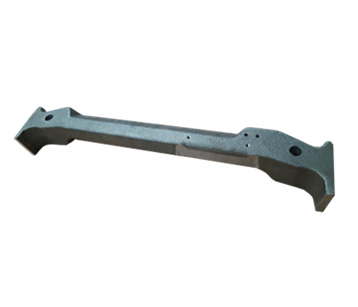
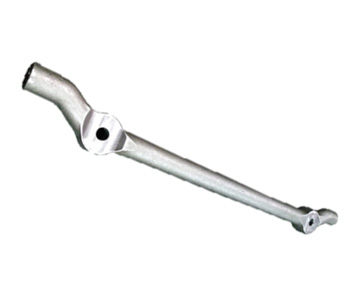
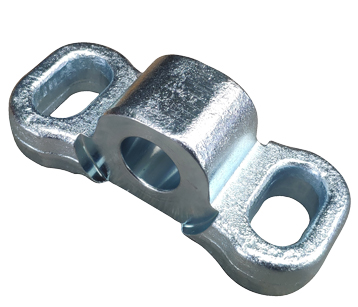
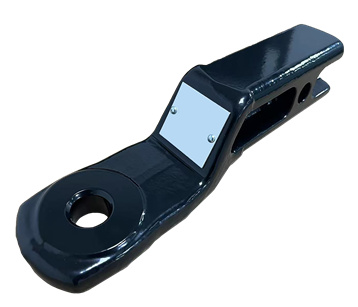